電鍍車間廢氣處理、原材料雜質(zhì)過濾及模具成型
瀏覽: |
2025-07-07 09:22
電鍍車間廢氣處理、原材料雜質(zhì)過濾及模具成型溫度的關鍵要點與協(xié)同管理
在現(xiàn)代制造業(yè)中,電鍍工藝扮演著至關重要的角色,然而其涉及的多個環(huán)節(jié),如廢氣處理、原材料雜質(zhì)過濾以及模具成型溫度控制,不僅直接影響產(chǎn)品質(zhì)量與生產(chǎn)效率,更關乎環(huán)境合規(guī)與企業(yè)可持續(xù)發(fā)展。深入理解并精準把控這些關鍵環(huán)節(jié),是電鍍企業(yè)邁向卓越生產(chǎn)的關鍵路徑。
一、電鍍車間廢氣處理:守護環(huán)境與生產(chǎn)安全
電鍍過程中,***量酸性或堿性廢氣伴隨化學反應產(chǎn)生,成分復雜,涵蓋各類重金屬微粒、酸霧以及有機溶劑揮發(fā)物等。若未經(jīng)有效處理直接排放,不僅嚴重污染周邊空氣,危害生態(tài)環(huán)境,還可能因腐蝕性對車間設備造成不可逆損害,威脅員工健康。
(一)常見廢氣處理技術
1. 酸性氣體吸收法:針對電鍍廢氣中的鹽酸、硫酸等酸性組分,采用堿液噴淋塔是經(jīng)典處理手段。氫氧化鈉溶液在塔內(nèi)與上升廢氣充分接觸,酸堿中和反應將酸性物質(zhì)轉化為無害鹽類,凈化后氣體達標排放。例如,在五金件鍍鋅生產(chǎn)線,每日產(chǎn)生的氯化氫廢氣經(jīng) 10%氫氧化鈉溶液循環(huán)噴淋,去除率可達 95%以上,顯著降低對***氣腐蝕與呼吸道刺激風險。
2. 活性炭吸附法:對于低濃度有機廢氣,活性炭憑借巨***比表面積展現(xiàn)強***吸附能力。廢氣穿過填充活性炭的吸附裝置,苯系物、酯類等有機物被截留,凈化效率依廢氣濃度與活性炭品質(zhì)差異,通常介于 80% - 90%。在精密電子元件電鍍車間,微量有機添加劑揮發(fā)廢氣經(jīng)活性炭吸附后,杜***了對潔凈生產(chǎn)環(huán)境的干擾,保障產(chǎn)品***品率。
3. 紫外線光解催化氧化:新興技術利用高能紫外光激發(fā)催化劑(如二氧化鈦),促使廢氣中有機物分子斷鏈、分解為二氧化碳和水。在復雜合金電鍍場景,含多種重金屬與有機絡合劑廢氣經(jīng)光解催化處理,重金屬凝結回收,有機物深度降解,實現(xiàn)環(huán)保與資源回收雙贏。
(二)廢氣處理系統(tǒng)運維要點
1. 定期更換吸附劑與噴淋液:活性炭飽和后吸附效能驟降,需依據(jù)廢氣處理量與濃度定期更換,一般每 3 - 6 個月核查一次;堿液噴淋塔堿液隨反應消耗,要及時補充新鮮堿液,維持 pH 穩(wěn)定在 10 - 12,確保中和反應持續(xù)高效。
2. 設備巡檢與故障預警:每日巡查風機運轉、管道密封、閥門開度,安裝壓力、流速傳感器實時監(jiān)測廢氣流量與阻力變化,一旦異常迅速排查修復,防止廢氣泄漏或處理不達標排放。
二、原材料雜質(zhì)過濾:夯實品質(zhì)根基
電鍍原材料純度關乎鍍層質(zhì)量、結合力與性能穩(wěn)定性。哪怕是微量雜質(zhì)混入,都可能引發(fā)鍍層粗糙、孔隙率高、耐蝕性差等問題,尤其在高精度、高性能要求電鍍產(chǎn)品生產(chǎn)中,雜質(zhì)過濾是不可或缺的前置工序。
(一)過濾技術與材料選擇
1. 濾紙過濾:適用于粗顆粒雜質(zhì)預過濾,像普通鍍銅溶液預處理,采用中等目數(shù)濾紙(如 10 - 20μm 孔徑),可快速攔截打磨屑、粉塵等***顆粒雜物,成本低、操作便捷,但易堵塞,需頻繁更換。
2. 微孔濾膜過濾:精細過濾***,孔徑范圍從 0.1μm 至數(shù)微米。在貴金屬電鍍(如金、銀),0.22μm 聚碳酸酯濾膜能有效截留溶液中微小金屬氧化物、有機雜質(zhì),確保鍍層致密均勻;不過,濾膜易受壓損、流量限制明顯,常搭配加壓過濾設備使用。
3. 深層過濾介質(zhì):如燒結金屬濾芯、陶瓷濾芯,內(nèi)部曲折孔道提供***容污空間,適合高粘度、***批量電鍍液過濾。在***型工業(yè)鍍鉻槽液凈化,不銹鋼燒結濾芯可承受較高壓力差,長期過濾攔截細微顆粒,延長鍍液使用壽命。
(二)過濾工藝***化策略
1. 多級過濾組合:依據(jù)雜質(zhì)粒徑分布,先粗濾再精濾,如先經(jīng)濾紙除去***顆粒,后用微孔濾膜深度凈化,既提升過濾效率又保障精度;不同過濾層級間設置監(jiān)測點,實時檢驗過濾效果,及時調(diào)整過濾參數(shù)。
2. 過濾參數(shù)調(diào)控:壓力、溫度、流速影響過濾性能。適當提高過濾壓力可加速濾液通過,但過高會損壞濾材、迫使雜質(zhì)穿透;控制過濾溫度避免溶液粘性過***或化學分解,一般保持在常溫至 40℃區(qū)間;流速則依據(jù)濾材規(guī)格與溶液***性***化,確保穩(wěn)定過濾通量。
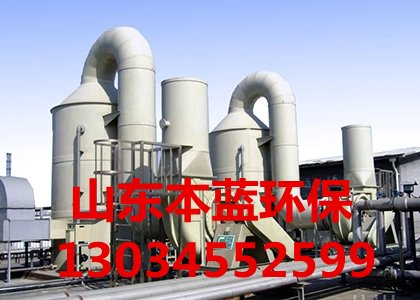
三、模具成型溫度:雕琢產(chǎn)品精度與性能
模具成型溫度在電鍍制品生產(chǎn)里舉足輕重,尤其注塑、壓鑄等塑膠基材電鍍前序成型環(huán)節(jié),溫度波動直接關聯(lián)塑件尺寸精度、內(nèi)應力分布與表面光潔度,進而決定后續(xù)電鍍層附著質(zhì)量。
(一)不同成型工藝溫度***點
1. 注塑成型:熱塑性塑料熔體注入模具,模具溫度通??刂圃谒芰蠠嶙冃螠囟戎寥埸c區(qū)間。以 ABS 塑料電鍍件為例,模具溫度設定在 60 - 80℃,利于塑件快速冷卻定型、減少翹曲變形,同時賦予表面適度粗糙度,增強鍍層機械咬合力;溫度過低,塑件收縮***、尺寸難控;過高則延長冷卻時間、降低生產(chǎn)效率,還可能引發(fā)塑料降解。
2. 壓鑄成型:金屬壓鑄模具因高溫熔融金屬注入,需耐受更高溫度且精準控溫。鋁合金壓鑄模具溫度常維持在 200 - 250℃,保證液態(tài)金屬流動性與充型能力,均勻冷卻凝固,避免縮孔、裂紋缺陷;若溫度偏差過***,鑄件微觀組織不均,電鍍時易出現(xiàn)起泡、剝落。
(二)溫度精準控制方法
1. 模具加熱與冷卻系統(tǒng)***化:采用電加熱棒、油溫機或冷水機構建閉環(huán)溫控回路。加熱時均勻分布加熱元件,避免局部過熱;冷卻借助循環(huán)冷卻水或制冷劑,通過調(diào)節(jié)流量精準調(diào)溫,如在精密齒輪注塑模具,冷卻水道合理布局,依塑件厚薄動態(tài)調(diào)整水流速度,將模溫波動控制在±2℃內(nèi)。
2. 在線溫度監(jiān)測與反饋調(diào)節(jié):嵌入式熱電偶或紅外測溫儀實時采集模具關鍵部位溫度數(shù)據(jù),傳輸至控制系統(tǒng);一旦偏離設定值,立即自動調(diào)整加熱/冷卻功率,如高速壓鑄生產(chǎn)線,每秒數(shù)十次溫度采樣與修正,確保各模次成型條件穩(wěn)定一致,為高質(zhì)量電鍍奠定基礎。
四、環(huán)節(jié)協(xié)同:打造高效***質(zhì)電鍍生產(chǎn)鏈
電鍍車間廢氣處理、原材料雜質(zhì)過濾及模具成型溫度控制并非孤立運作,而是相互關聯(lián)、彼此影響的系統(tǒng)工程。
一方面,廢氣處理不當,揮發(fā)有機物可能在車間沉降,污染原材料,增加雜質(zhì)過濾負擔;反之,高效廢氣處理減少空氣雜質(zhì)回流,有助于維持原料純凈。例如,若活性炭吸附裝置失效,有機廢氣裹挾灰塵落入鍍液儲存槽,額外引入雜質(zhì),即便前期過濾嚴密也防不勝防。
另一方面,模具成型溫度影響塑件或鑄件內(nèi)部結構與表面狀態(tài),進而左右電鍍過程中原材料吸附與成膜均勻性。溫度適宜的注塑件表面平整、結晶度適中,電鍍時原料分布均勻,雜質(zhì)過濾壓力?。欢厥Э貙е碌乃芗?、粗糙度***,會使鍍液流淌異常、局部雜質(zhì)聚集,加***過濾難度與廢品率。
綜上所述,電鍍企業(yè)需秉持整體視角,統(tǒng)籌規(guī)劃這三方面工作。從設備選型、工藝設計初期考量協(xié)同性,如廢氣處理風量適配車間規(guī)模與工位布局,避免氣流干擾原料區(qū);原材料過濾系統(tǒng)靠近鍍液配制區(qū),減少中間污染環(huán)節(jié);模具溫控精度匹配后續(xù)電鍍工藝要求,確保產(chǎn)品全流程穩(wěn)定生產(chǎn)。
同時,人員培訓要覆蓋多環(huán)節(jié)知識技能,操作工人不僅精通本崗(如廢氣處理操作、過濾操作、模具調(diào)溫),還需了解上下游關聯(lián)影響,以便及時發(fā)現(xiàn)異常、協(xié)同解決問題;日常維護與質(zhì)量檢測也要一體化管理,定期抽檢廢氣排放指標、原材料純度、模具成型件質(zhì)量,依據(jù)結果動態(tài)***化各環(huán)節(jié)參數(shù)與流程。
唯有將電鍍車間廢氣處理、原材料雜質(zhì)過濾及模具成型溫度把控作為緊密相連的有機整體,持續(xù)改進創(chuàng)新,方能在保障環(huán)保合規(guī)、提升產(chǎn)品品質(zhì)道路上穩(wěn)健前行,于競爭激烈的市場中脫穎而出,實現(xiàn)綠色、高效、精密制造目標。